By: Aaron Watson – Tool Maker at HTI Plastics
What is Tool (Mold) Maintenance?
At HTI, we classify Tool Maintenance in two categories: Repair and Preventative.
Tool maintenance repairs happen when something breaks or is damaged during the molding process and creates a product that is outside of specifications or quality standards. Our Toolroom staff makes the necessary repairs to get the mold back in working order by using a multitude of machines and tools to either build new components, weld and machine the damaged part back into original condition, or replace with spare components that we have on hand.
Preventative tool maintenance (PM) is a type of maintenance done at certain intervals, usually shot/cycle counts. It starts by inspecting the tooling and product to make sure things are not wearing out prematurely, and everything is in place to produce a quality product for our customers on time. We have 3 different levels of PM’s here at HTI: Clean and Grease, General, and Major. Think of PM’s like getting the oil changed in your car and multipoint safety inspection at the same time.
What are the parts of a mold? (Picture)
Every mold is different and has different components, but there are some standard components that we inspect on every mold during a PM.
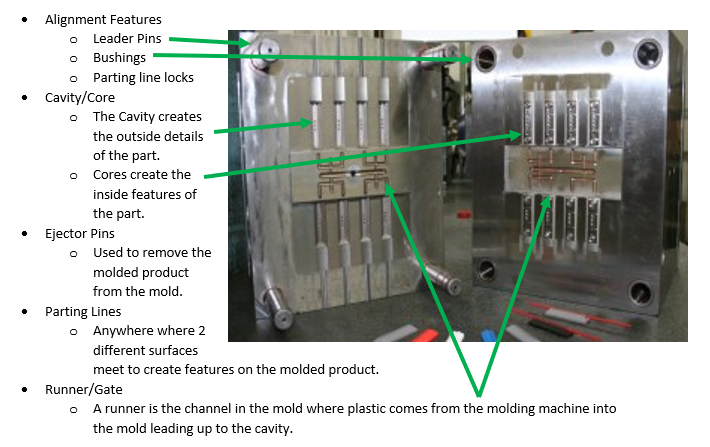
- Vents/Vent Dump
o Vents allow air to escape from the cavity so the plastic can take its place and make a complete part. These are usually .0005” – .002” deep depending on the material being molded. Deep enough for air to escape but not let plastic escape from the cavity.
o Vent dumps allow the air to escape faster, they are much deeper and generally connect multiple vents together. They are usually .010” -.020” deep and go out to the atmosphere.
Why is tool (mold) maintenance important?
Proper tool maintenance repairs is important to help us supply quality products and reduce downtime from potential mold-related issues. By getting ahead of issues before the tool is scheduled to run, we avoid delays from unscheduled downtime on the press. Our PMs also allow us to set targets during long production runs. By setting these targets, we can know when to pull the mold out for scheduled maintenance before something major happens, like producing parts out of specification, or before the mold breaks to a point of creating costly repairs.
Clean and Grease
The process of clean and greases are our lowest form of PM. This is not done on every mold but is completed on molds that require more frequent attention, due to the complexity of the material used to produce a part. Some resins create more gases and build-up, requiring the mold to be cleaned more often. We clean the mold parting line and apply proper lubrication to moving components. We also check for damage and wear that would affect the mold’s operation and the part’s integrity. This simple maintenance can be done while the mold is in the press. General frequency is anywhere from 5,000 cycles to 50,000 cycles
General Maintenance
Depending on the complexity of the mold, larger-scale general maintenance is usually done according to cycle count, or the number of times the mold has been run. Basic open-and-shut molds without complex action receive general maintenance between 250,000 and 500,000 cycles. A mold with many moving parts requires a closer look, so we do general maintenance every 100,000 cycles.
We inspect the last shot of parts from the mold for damage or defects. If all is well, we go ahead and disassemble the mold completely. The mold plates are cleaned and inspected for signs of wear, vent depths are checked, and O-rings are replaced. Any part of the mold that is defective or damaged is repaired. If the mold is equipped with a hot runner, we check it for signs of leakage and inspect the condition of the components. Then, we reassemble the mold, run a thorough systems check, and ready it for production or storage.
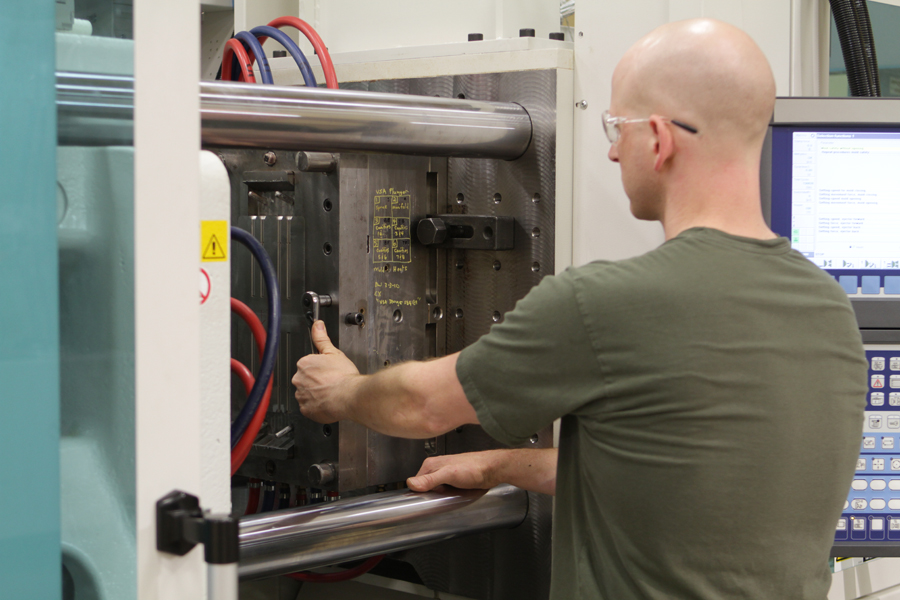
Major Maintenance
Every mold undergoes major preventative maintenance, between 500,000 and 1 million cycles. This process includes all of the steps done in general maintenance and takes a much more in-depth look. We measure the mold’s alignment features, compare them to their baseline “new” condition, and replace them as necessary. All other components are measured to the original print dimensions and put back to new condition. We clean every water passage in the mold by removing all pipe plugs, baffles, and water fittings. If the mold cavity finish is degraded at all, we refurbish it. When all’s said and done, we rebuild the mold in better-than-new conditions and put it back to work!
If you have additional questions about your tool care and maintenance, or any of the other services offered by HTI Plastics, please contact us at through our website www.htiplastic.com, or at 1-800-824-0607.