HTI Plastics Helps Lincoln Composites Expand
into Fuel Alternatives Market
Many American market sectors are increasingly impacted by our country’s urgent need to attain energy security by finding viable, affordable alternatives. The cost savings of natural gas makes it a major option in the search for alternative fuel for vehicles, and the natural gas market presents high profit potential. HTI customer Lincoln Composites made a decision some time ago to focus on natural gas and take advantage of that potential. Through ingenuity and persistence, the company has continually expanded its position in fuel cylinders over the past nearly seven decades.
Since its 1963 beginning as a supplier of filament-wound structures for the defense industry, Lincoln Composites has worked to commercialize the fabrication process, eventually commanding notable impact in natural gas and hydrogen fuel cylinders in the North American fuel cell market. As a result, the company’s sales revenues have grown by a factor of 10 between 2005 and 2012. Today, Lincoln Composites is the largest composite fuel cylinder company in the world.
Over the years, HTI Plastics has developed a solid partnership with Lincoln Composites as its primary supplier of injection molded liners for fuel cell cylinders. The units are manufactured in approximately 10 different diameters, with many more configurations within each diameter. A liner is comprised of two domes, with an extruded tube between HTI Plastics Molded Plastic Partthem. Its function is to create a gas barrier, gas connections for the cylinder, and a mandrel to filament-wind the carbon/fiberglass composite. A typical fuel cylinder can operate at up to 3,600 psig, while hydrogen fuel cells operate at up to 10,000 psig.
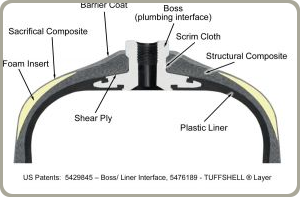
Lincoln Composites recently invested in a large-tonnage mold machine and located it at the HTI Plastics facility. Given the direction the company plans to go in the future (larger press), and the powerful partnership it has developed with HTI over the years, it was an easy decision to make the investment.
From a standpoint of expertise, capability, acuity and logistics, HTI provided a key advantage to Lincoln Composites, not only helping the company identify opportunities for and implement major cost savings, but also providing close teamwork, daily collaboration, and experienced product development that enhanced Lincoln Composites’ strategies and methods. Lincoln Composites and HTI Plastics work together to evaluate new manufacturing processes and materials with the same goal: to offer the market exceptional parts to meet customer needs.
“Lincoln Composites and HTI have partnered for years, and the team approach has been fruitful for both companies,” said Jack Schimenti, Lincoln Composites’ President. “We regularly sit down with each other to work out everyone’s needs and desires. Then we collaborate to limit the scheduling and cost impact while meeting strict requirements for our products. It just can’t be done any other way.”
What does the future hold for Lincoln Composites in fuel cells? The company expects a growth rate of more than 30% over the coming years—a more-than-respectable return on investment in any market segment.