Importance of Manufacturing Regulations
HTI compliance assures quality.
Early in manufacturing, when devices were poorly designed or constructed (as they often were), there was little recourse. Today, consumers don’t worry as much about poor manufacturing thanks to regulations all manufacturers must follow. Today’s manufacturers don’t mind following regulations, because it proves quality.
In plastics, an important U.S. Food and Drug Administration (FDA) regulation assures the safety, effectiveness and purity of products. Regulations for different industries vary. They must be interpreted and applied in accordance with device type and assessed risk. For medical devices, production control steps will be more thorough for dialysis equipment than for simple devices like tongue depressors. To comply, each organization determines appropriate control levels for their products.
Regulation-Related Efficiency and Adaptability Assure Quality
The better defined a process, the less components cost. Plastic injection molded parts generally are designed to be inexpensive. Highly-efficient processes require less expense for inspection and testing than less-efficient processes producing many nonconforming products.
FDA Compliance 21 CFR 820 Quality System Regulation Guides Outcomes
HTI has a six-person quality staff, but all personnel are trained in quality processes, procedures, defect recognition, and regulations. Production is regulated by the FDA Compliance 21 CFR 820 Quality System Regulation. This requires HTI to have a quality management system designed tomeet the regulation. The regulation doesn’t dictate process. It gives all manufactures freedom to build processes that make sense. This regulation describes outcomes and requires manufacturers to be consistent with the description, but leaves interpretation and method of compliance up to each manufacturer.
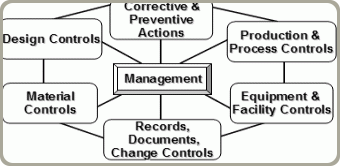
HTI has made several changes to comply with this regulation and ensure quality, including: a clean assembly area free of wood or cardboard, to reduce contamination; specific requirements for gowning and handling of FDA products; procedures for internal auditing of processes to evaluate effectiveness; and procedures for product recall and the reporting of adverse events to the FDA, just to name a few.
HTI and employees benefit in a different way. Regulated customers must give us uniform operating expectations which minimize liability. HTI employees, who are trained, can reference documented procedures any time, which helps reduce job loss due to catastrophic events.
Voluntary ISO 13485:2016 Certification Requires Deep Commitment
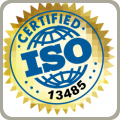
In addition to FDA compliance, HTI earned a voluntary ISO 13485:2016 certification not every manufacture can claim. To get it, HTI designed and implemented a Quality Management System meeting ISO criteria, passed an extensive third-party audit, and sustains annual surveillance audits. According to Rob White, HTI Quality Manager, certification to the ISO standard is becoming common among committed medical device molders. Among companies of HTI’s size and flexibility, however, it is still a somewhat unique accomplishment.
ISO 13485 certification also benefits HTI customers and employees. Customers know they are dealing with a molder very familiar with the challenges they face. Customers can be confident HTI has committed significant time and resources to designing a quality manufacturing system and delivering quality devices. ISO certification gives HTI and its employees instant credibility when talking with medical device manufacturing prospects.
Beyond Regulation and Certification: Dedication to Excellence
HTI has invested enormous amounts of time, equipment and personnel to successfully producing products and following regulations. We constantly look for ways to improve processes and products, and are committed to exceeding expectations. Though regulations play an enormous part in plastics manufacturing, we know it’s up to us to set the standard of excellence.